Introduction
Some bearings may be small, but they keep machinery running effectively—reducing friction, supporting heavy loads, and ensuring optimal performance. Yet, many industries only notice a problem when a bearing fails—often leading to unexpected downtime, inefficient processes, and expensive repairs.
At RPM, we believe most bearing failures are preventable by adopting the right maintenance practices and using advanced tools. In this guide, we share our practical dos and don’ts, complete with real-world examples and insights from our inventory and technical teams.
The Dos Of Bearing Maintenance
1. Always Use the Right Lubricant
Lubrication is the first line of defense against bearing failure. Without the proper lubricant, friction rises, wear accelerates, and failure becomes inevitable. Here’s how to do it right:
- Choose Quality. Use high-grade lubricants from trusted brands like SKF.
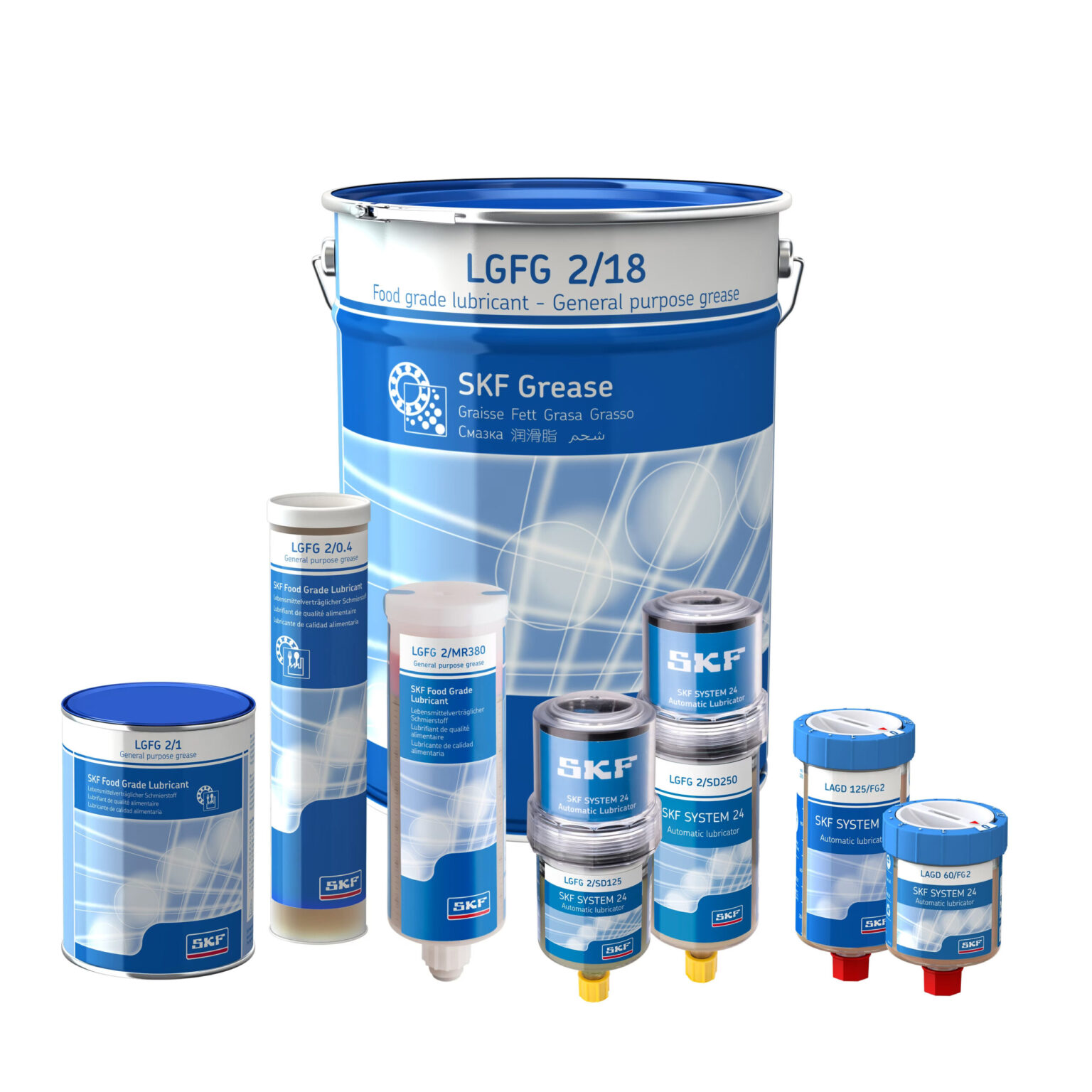
- Monitor Lubricant Levels. Maintaining the correct lubricant level is crucial. We recommend using advanced tools such as the SKF Lubrication Analyzer. This automated system continuously checks lubricant levels and quality, ensuring optimal performance and preventing the risks associated with both under- and over-lubrication.
AUTOMATIC LUBRICATION SYSTEM & SKF MICROLOG ANALYZER
- Follow Compatibility Guidelines. Avoid mixing lubricants unless they’re proven to work well together. Using the correct lubricant formulation for your specific application is key to reducing wear.
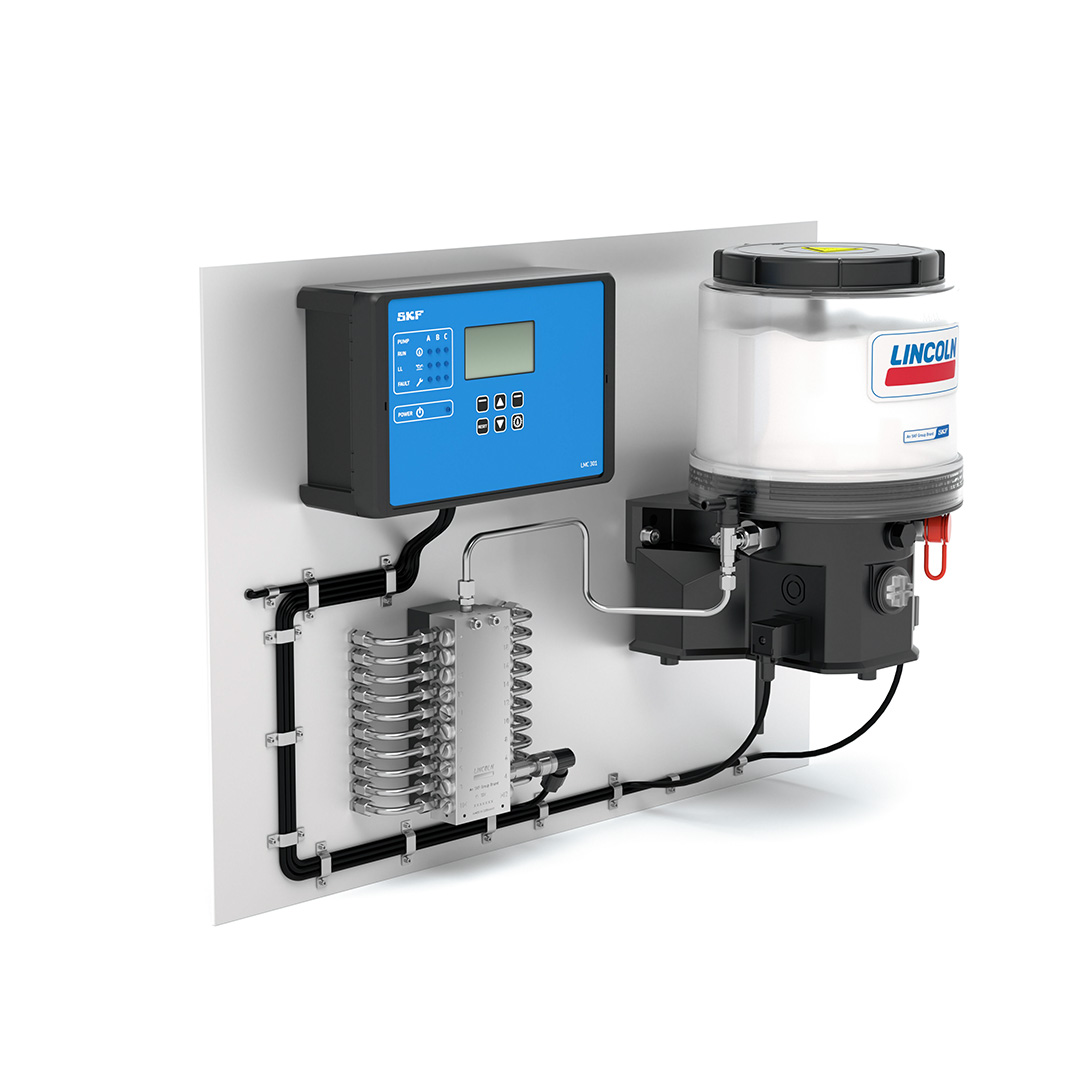
2. Mount Bearings The Right Way
Improper mounting is one of the leading causes of bearing failure. Incorrect mounting can lead to uneven load distribution and early failure. We recommend adhering to these practices to ensure a flawless installation:
-
Use Specialized Tools: Utilize SKF’s bearing fitting toolkit to guarantee precise alignment and even load distribution.
-
Follow Manufacturer Guidelines: Always adhere to the installation procedures recommended by the bearing manufacturer. This minimizes the risk of misalignment and extends the service life of the bearing


3. Handle Bearings with Care
Even the highest-quality bearings are susceptible to damage if mishandled. Proper handling and storage are just as important as installation:
-
Controlled Storage: At RPM, we maintain a dedicated inventory system where bearings are stored in climate-controlled environments. This protects them from contaminants and environmental damage.
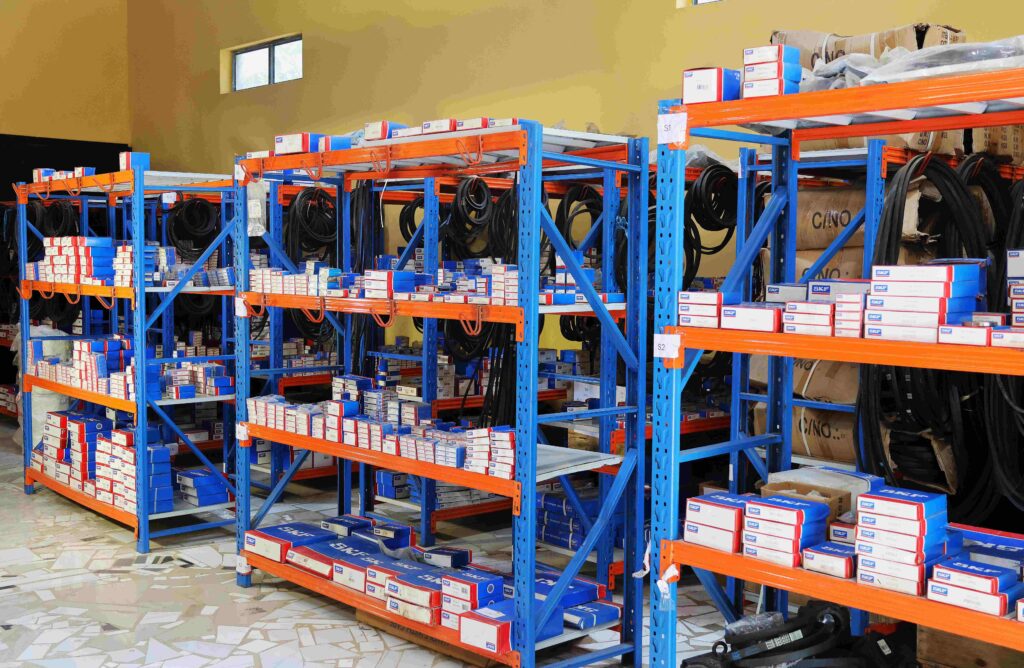
-
Careful Handling: Bearings are kept in their original protective packaging until they are ready for installation or delivery to a client’s factory or Plant. Our supplychain and inventory staff are trained in proper handling techniques to minimize contamination and physical damage during transport and storage.
4. Conduct Regular Inspections
Routine inspections can help detect early signs of wear before they escalate:
-
What to Look For: Regularly check for signs of wear, misalignment, unusual noises, or overheating.
-
Proactive Service: RPM’s projects arm, CaTS, offers scheduled inspection services using advanced diagnostic tools to identify potential issues early. Early intervention can save significant repair costs and prevent unscheduled downtime.
5. Monitor Operating Conditions
Bearings perform best within specific temperature, load, and speed ranges. Exceeding these limits accelerates wear and increases the risk of failure.
-
Use Real-Time Monitoring: Employ vibration and temperature sensors to continuously monitor operating conditions. RPM offers sensors from top manufacturers like SKF to offer systems that alert you to anomalies before they become critical.
- Maintain Optimal Parameters: Ensure your machinery operates within the recommended ranges to protect your bearings and optimize performance.
The Don’ts: What to Avoid
Maintaining bearings isn’t just about what you do—it is also about what you avoid:
-
Don’t Mix Incompatible Lubricants: Randomly combining lubricants can compromise bearing performance. Stick with proven, trusted products.
-
Avoid Unclean Environments: Dust, debris, and moisture are bearing enemies. Keep your work area clean and controlled.
-
Don’t Ignore Warning Signs: Unusual noises, vibrations, or excessive heat are indicators of potential issues. Address them immediately to prevent further damage.
-
Never Overlook Corrosion: Rust and corrosion increase friction and reduce efficiency. Replace or repair affected bearings as soon as corrosion is detected.
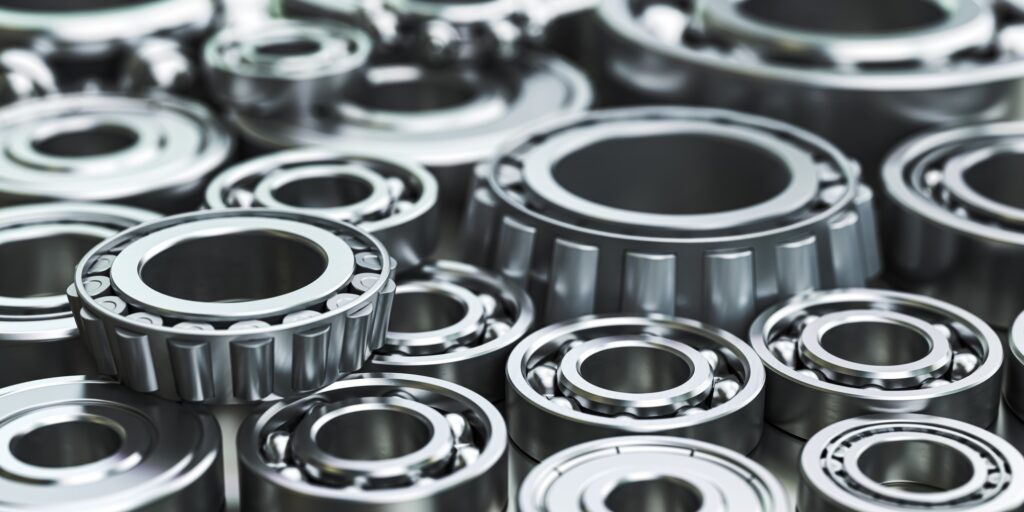
Industry-Specific Applications
In sectors like manufacturing, mining, power generation, and beyond, a single bearing failure can halt an entire production line and lead to significant financial losses. RPM partners with industry leaders like SKF to support these industries by:
-
Stocking Quality Parts: We maintain a robust inventory of high-quality bearings and lubricants to ensure you have the right components when you need them.
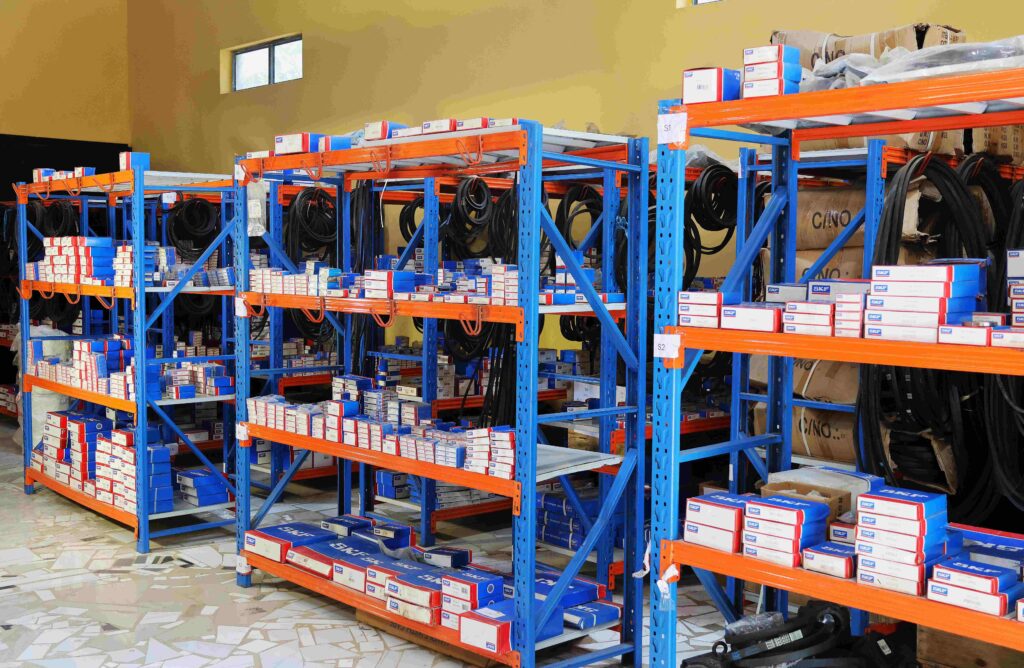
-
Offering Expert Consultation: Our technical team provides onsite support and practical advice to help you optimize your bearing maintenance practices.
-
Tailoring Solutions: We work closely with industry leaders like SKF to deliver customized solutions that meet the unique challenges of your operations.
For more information on our products and services, please visit our Products Page.
Conclusion
Effective bearing maintenance is not rocket science; it just requires consistency, attention to detail, and the right tools. By following these best practices and leveraging advanced solutions like SKF’s Lubrication Analyzer and mounting systems, you can extend bearing lifespan, reduce downtime, and keep your operations running as they should.
For expert guidance or to schedule an inspection, contact us at [email protected] or call 0803 6089 098.