Introduction
Whether you’re looking to enhance the efficiency of your manufacturing processes, improve the performance of your machinery, or increase the overall productivity of your facility, selecting the right gearmotor is crucial. But with so many options available on the market, it can be overwhelming to know where to start. This comprehensive guide will help you understand the different types of gearmotors, their applications, and the key factors to consider when making your selection. From torque and speed requirements to environmental factors and maintenance considerations, we’ve got you covered.
If you’re ready to make an informed decision that will drive your industrial operations to new heights, explore this ultimate guide to choosing the right gearmotor for your industrial needs.
Understanding the Importance of Choosing the Right Gearmotor
Choosing the right gearmotor is like picking the perfect pair of shoes. Too tight, and your feet hurt. Too loose, and you’re left stumbling all over the place. A gearmotor is a power transmission device that combines an electric motor with a gear reducer, converting electrical energy into mechanical energy to power your machinery. The performance of your machinery and the efficiency of your manufacturing processes heavily depend on the gearmotor you choose.
A well-matched gearmotor ensures smooth operations and peak efficiency, while an ill-suited one can cause headaches, inefficiencies, and higher maintenance costs. By selecting the right gearmotor, you can optimize your operations, reduce energy consumption, improve productivity, and extend the lifespan of your machinery. With the right gearmotor, higher torque, precise control and increased speed can be achieved all while minimizing noise and vibration levels.
Factors to Consider When Selecting a Gearmotor
Selecting the right gearmotor involves considering several important factors specific to your industrial application. Think of this as whipping up the perfect burger; every layer of ingredient matters.
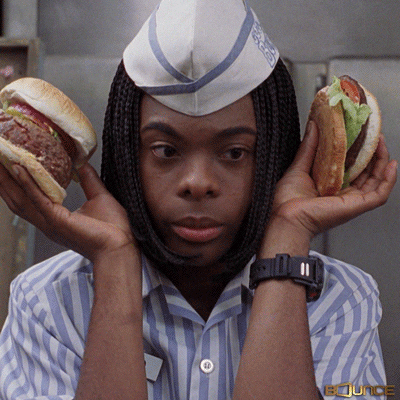
Torque and Speed Requirements
First, determine the torque and speed requirements of your machinery. Torque is the rotational force produced by the gearmotor, while speed refers to the rotational velocity. These two factors are crucial for performance. These two factors are crucial in determining the performance capabilities of the gearmotor and must be carefully matched to your specific application.
Environmental Conditions
Next, consider the environmental conditions in which the gearmotors will operate. Temperature, humidity, dust, and exposure to chemicals can impact the performance and lifespan of the gearmotor. Select a gearmotor that can withstand these conditions to ensure optimal performance and longevity.
Maintenance Requirements
Maintenance is another key factor. Some gearmotors require regular lubrication or periodic checks, while others are maintenance-free. Depending on your resources and operational needs, pick a gearmotor that fits your maintenance capabilities. Or you can simply contact RPM for the perfect pick on gearmotors and more.
Service Factor
Finally, take the service factor into account. The service factor in this case, is a measure of your gearmotor’s capacity to handle occasional overloads or harsh operating conditions. A higher service factor means the gearmotor can handle more demanding applications without compromising on its performance or lifespan. Ensuring the right service factor for your application will provide an extra buffer against unexpected breakdowns.
Selecting the right gearmotor might seem daunting, but with these factors in mind, you can make a well-informed decision. Or you can simply contact RPM for the perfect pick on gearmotors and more.
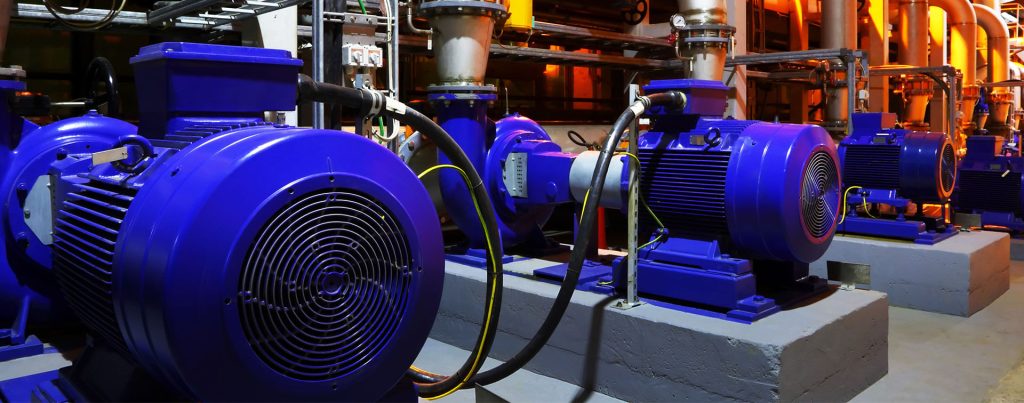
Different Types of Gearmotors and Their Applications
Gearmotors come in various types, each with its own unique characteristics and applications. Understanding the differences can help you narrow down your options and choose the most suitable one for your industrial needs.
Helical Gearmotors
Helical gearmotors feature helical gears that provide smooth and quiet operation. Perfect for applications where noise reduction is crucial, like conveyor systems, mixers, and pumps. These can easily be referred to as the noise-canceling headphones of gearmotors.
Worm Gearmotors
Worm gearmotors consist of a worm gear and a worm wheel, known for their high torque capablities and compact design. Ideal for elevators, winches, and conveyors. They are the compact SUVs – powerful, yet space-efficient.
Planetary Gearmotors
Planetary gearmotors are another popular choice, especially in applications that require high torque and precision. With multiple planetary gears distributing the load, they offer excellent power transmission efficiency. Commonly found in robotics, packaging machinery, and CNC machines, they can be likened to the perfect Swiss watches of gearmotors—precise and ever reliable.
Calculating Torque and Speed Requirements for Your Industrial Needs
Calculating the torque and speed requirements for your industrial needs is crucial. Torque depends on the load that the gearmotor needs to move, while speed is influenced by the desired operational speed of your machinery.
In calculating the torque requirement, factors such as the load weight, distance and any friction or resistance present need to be carefully considered. The speed requirement, however, depends on the specific application and desired operational speed. Accurate calculations ensure that the gearmotor can handle the load and operate smoothly.
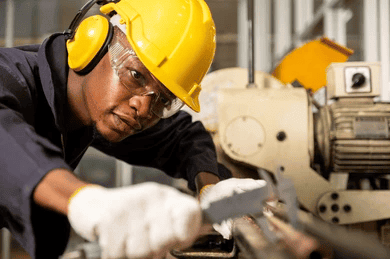
Evaluating Gearmotor Efficiency and Power Transmission Capabilities
Efficiency is key when selecting a gearmotor for your industrial needs. It refers to how effectively it converts electrical energy into mechanical energy. A more efficient gearmotor means less wasted energy and lower operating costs.
Power transmission capabilities are also crucial. This refers to how well the gearmotor transmits power from the motor to the driven load. A gearmotor with high power transmission capabilities will minimize energy losses and ensure smooth, reliable operation.
Additionally, incorporating Variable Frequency Drives (VFDs) can also enhance energy savings. These allow for precise control of motor speed, adjusting power usage to match load requirements, thus reducing energy consumption and operational costs. When evaluating these factors, it is essential to look at the gear ratio, which determines the relationship between speed and torque output of the gearmotor.
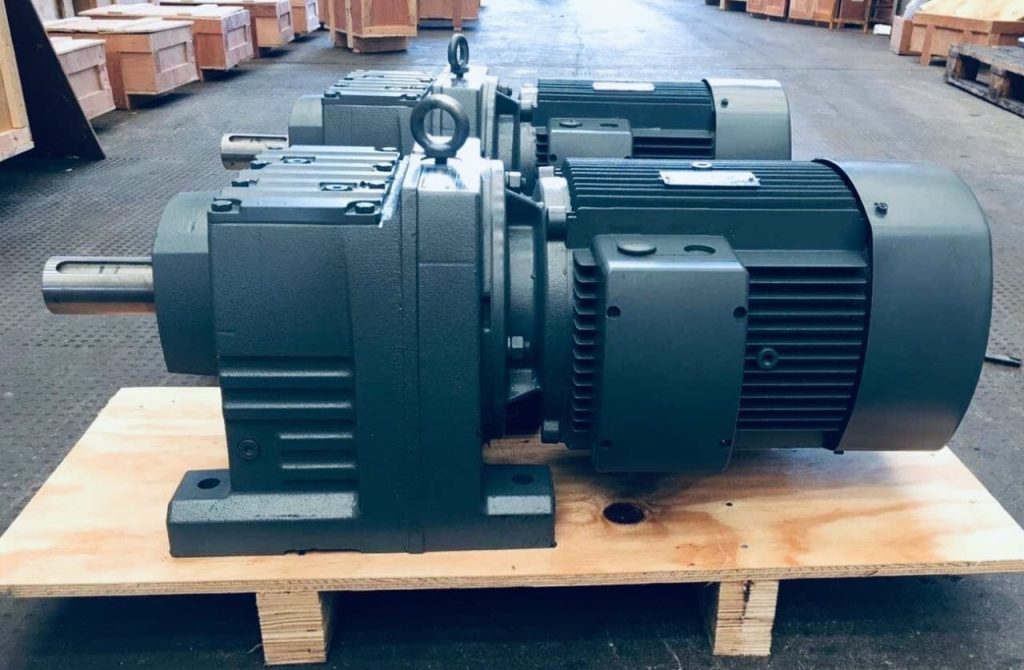
Choosing the Right Gear Ratio for Optimal Performance
The gear ratio determines the relationship between the speed and torque output of your gearmotor. A higher gear ratio provides higher torque output but lower speed, while a lower gear ratio offers higher speed but lower torque. It’s all about finding the right balance that suits your specific application requirements.
Additionally, you should consider the efficiency and power transmission capabilities of the gearmotor at different gear ratios to ensure optimal performance.
Considerations for Gearmotor Installation and Maintenance
Proper installation and maintenance are essential for long-term performance and reliability. When installing your gearmotor, ensure proper alignment between the motor and the driven load to prevent wear and tear which will lead to decreased efficiency and eventually, premature failure. Regular maintenance checks can catch potential issues early and prevent costly breakdowns.
Depending on the type of gearmotor, maintenance requirements may vary. Some gearmotors require regular lubrication, while others are sealed and maintenance-free. Follow the manufacturer’s guidelines for maintenance, and monitor the operating conditions to address any environmental factors that may impact performance. This can be quite similar to running routine checks on your car to keep it running smoothly.
Popular Gearmotor Manufacturers and Their Product Offerings
When choosing a gearmotor, consider reputable manufacturers known for high-quality products and reliable support. Here are some industry leaders:
Nord DriveSystems: Nord is a well-known manufacturer of gearmotors and drive solutions, with a focus on energy efficiency and reliability. They offer a wide range of gearmotors, including helical, worm, and bevel gearmotors, designed for various industrial applications.
Baldor : Part of the ABB Group, Baldor is a renowned manufacturer of electric motors and gearmotors. They provide a comprehensive range of gearmotors designed for different industries, including helical, worm, and parallel shaft gearmotors.
Bonfiglioli : A leading manufacturer of gearmotors, gearboxes, and drive systems. They offer a diverse portfolio of gearmotors, including helical, worm, and planetary gearmotors, suitable for a wide range of industrial applications.
IMAK: Known for its innovative gearmotor solutions that combine high performance with durability. Their product offerings include helical, bevel, worm gearmotors among others, all designed to meet the demanding requirements of various industrial sectors.
WEG: WEG is a global leader in the manufacturing of electric motors and gearmotors, offering robust and efficient solutions for industrial applications. Their range includes helical, parallel shaft, and bevel gearmotors, known for their reliability and performance.
Other top manufacturers include: Motovario, SEW Eurodrive, Sumitomo, Rossi, Bauer among others.
Have a request for any of the above?
Conclusion: Making the Right Decision for Your Industrial Gearmotor Needs
Choosing the perfect gearmotor for your industrial needs is a big decision. By understanding the key factors and points enunciated above, you can make an informed decision that will help optimize your industrial operations.
With this ultimate guide, you can confidently navigate the vast array of options and select the ideal gearmotor to enhance the efficiency, performance, and productivity of your industrial operations.
RPM is here to guide and inform your decisions towards elevating overall output and operations. Reach out for your customized industrial solutions today