Excessive noise or vibration, poor performance, engine failure, leaking process fluids, giving off higher than normal heat are all signs of an imminent pump failure.
Once the pump starts to malfunction, the problem will only get worse over time. Issues with the pump can cause damage to both the pump itself and to downstream equipment, which will likely cause more problems.
It is important to inspect all the components for abnormal wear and tear, especially in the bearings, couplings, and seals. They are the most common pump components and account for thousands of dollars in maintenance costs annually.
With over a decade of experience in the engineering industry, we know how to prevent and fix faulty components and assemblies. Here are some ways to detect parts failures, identify the root causes of them, and avoid them in the future.
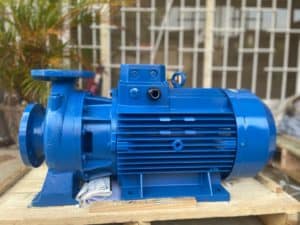
1) Listen for clicking, squealing, rumbling, or unusual noise. If you hear any of these sounds, you’re hearing the warning signs that your bearings are about to fail. Early indications of bearing problems include noise, high temperature, and high vibration.
2) While bearings are usually lubricated at the factory, you may need to lubricate them differently depending on how they’re used. (Sealed bearings are one exception to this.) Failing to keep bearings properly lubricated may lead to overheating and failure. A proper lubrication schedule is essential for the operation of pumps.
3) In addition to lubricant contaminants, some other threats to the proper operation of bearings include grit and other contaminants as well as misalignment and vibration. In some cases, this causes spalling and damage to the bearing surface over time.
1) When the pump shaft is out of alignment with the motor shaft, the coupling fails, this is often due to improperly installing the shafts or because of vibration. If you see black debris or shavings when looking under the coupling, it may be time to move on.
2) If the vibrations of a pump are not within the normal range during regular operation, it may indicate a misalignment of the pump.
3) Whenever troubleshooting is necessary, always check coupling alignment right before you repair the pump. Also, verify alignment after you’ve started the pump or when it’s warmed up.
4) To align a parallel coupling, place a straightedge across the two corners of the coupling’s hexagon and measure how much it is misaligned. If there is a large amount of misalignment, then it needs to be realigned.
After parallel alignment of the coupling, the angular alignment should then be checked with a micrometer or caliper. Measure from the outside of one flange to the outside of the other at intervals around the periphery of the coupling.
1) Failure of mechanical seals is usually easy to spot, with a slow drip or steady stream of fluid sprouting from the seal gland. Such a failure is seldom the cause of equipment failure, but it can be a warning sign of other problems.
2) Poor material selection is a common mistake. It can lead to seals swelling or cracking or corrosion of the face. While most people know that you need a robust seal for corrosive fluid, many fail to take into consideration conditions such as temperature.
3) If a pump is operated too quickly, a crack might develop in the pump’s seal. But there are other factors as well. The pump’s operating conditions also have an impact on its performance and lifetime.
4) If your seal must withstand extreme temperatures, you should understand how the operating conditions affect the seal. If the fluid’s temperature is extreme, the seal may crack.
After parallel alignment of the coupling, the angular alignment should then be checked with a micrometer or caliper. Measure from the outside of one flange to the outside of the other at intervals around the periphery of the coupling.
When seals fail, it is most often due to dry running. Dry running can be caused by issues with the fluid source, blockages in the suction side of the pump, or the pump running with its discharge closed. thermally triggered the dry running of a pressurized hydraulic system can cause unexpected seal damage.