Introduction
In the fast-paced world of manufacturing, keeping production lines running smoothly is paramount. Unplanned downtime due to a lack of critical spare parts can be incredibly costly, impacting everything from production schedules to customer satisfaction. Effective spare parts inventory management is a cornerstone of operational excellence, ensuring the right parts are available at the right time to prevent disruptions.
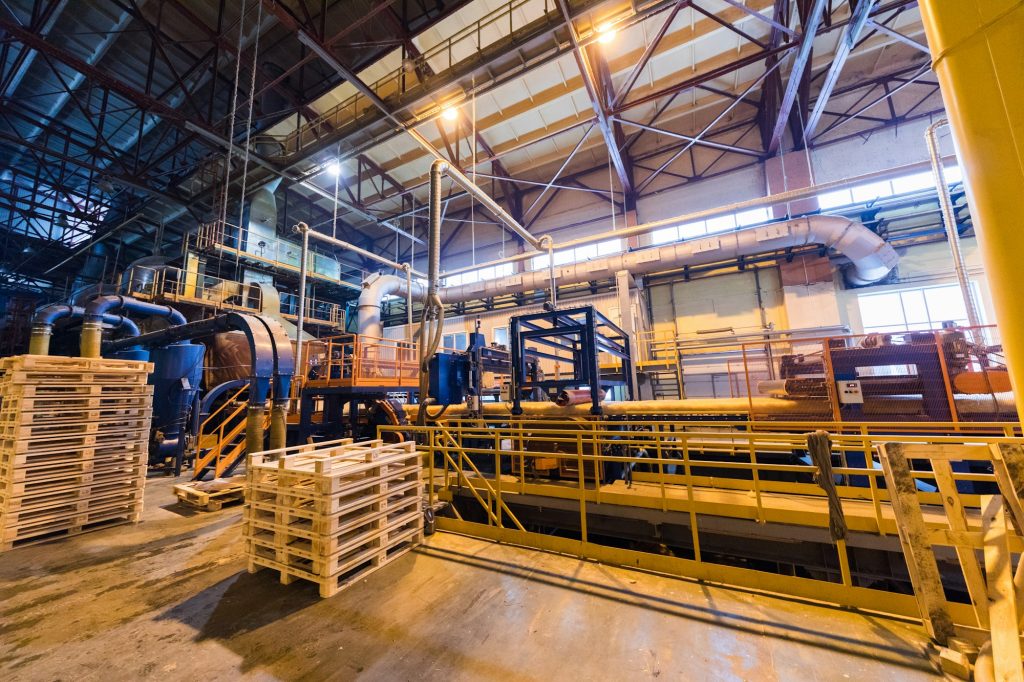
This comprehensive guide dives deep into seven best practices for spare parts inventory management in manufacturing industries. By implementing these strategies, you can optimize your spare parts inventory, minimize downtime, and achieve significant cost savings.
Importance of Spare Parts Inventory Management in Factories
Spare parts, also known as industrial spares, are essential components held in reserve to maintain and repair equipment breakdowns within a manufacturing facility. Effective spare part inventory management offers a multitude of benefits, including:
- Reduced Downtime: Having readily available spare parts allows for prompt repairs, minimizing production line stoppages and delays in fulfilling customer orders.
- Enhanced Operational Efficiency: Streamlined inventory management processes decrease time spent searching for or ordering parts, allowing maintenance teams to focus on preventative measures and repairs.
- Cost Optimization: By optimizing stock levels, you can minimize unnecessary storage costs and avoid the risk of obsolete parts becoming unusable and needing disposal.
- Improved Equipment Lifespan: Regular maintenance and repairs using appropriate spare parts help extend the lifespan of valuable machinery, reducing capital expenditure needs for equipment replacements.
- Enhanced Safety: With essential parts readily available, repairs can be completed swiftly, mitigating potential safety hazards associated with malfunctioning equipment.
Common Challenges in Spare Parts Inventory Management in Factories
Despite the undeniable importance of effective spare parts management, several challenges can hinder its successful implementation:
- Inaccurate Inventory Data: Incorrect or outdated inventory data can lead to stockouts on critical parts or overstocking of rarely used items.
- Lack of Standardization: Unstandardized parts across different equipment types can complicate ordering and storage processes.
- Unforeseen Equipment Failures: Sudden breakdowns of unexpected severity can expose gaps in spare parts planning.
- Limited Storage Space: Manufacturing facilities often have limited storage capacity, requiring careful consideration of storage optimization for spare parts.
- Inefficient Replenishment Strategies: Reactive ordering practices, triggered by part depletion, can lead to delays in acquiring critical spares.
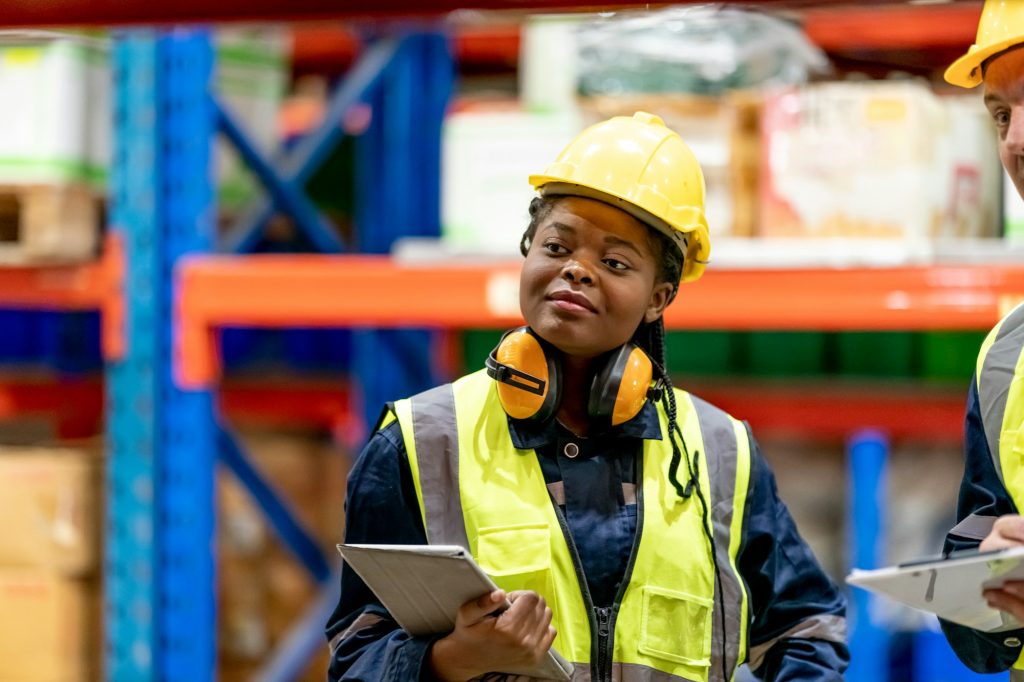
Best Practices For Spare Part Inventory Management
1: Conducting a Thorough Inventory Audit
The foundation of effective spare parts management rests on having a clear understanding of your existing inventory. A comprehensive inventory audit involves physically verifying and documenting the following details for each spare part:
- Part Number: Unique identifier for ordering and tracking purposes.
- Description: Clear and concise description of the part’s function.
- Quantity on Hand: Actual number of each part currently in stock.
- Minimum Stock Level (Safety Stock): The minimum quantity required to avoid stockouts during lead times for acquiring new parts.
- Maximum Stock Level: The upper limit for stocking a particular part to avoid overspending and tying up capital in rarely used spares.
- Location: Physical location within the warehouse or storage facility.
- Lead Time: Estimated time required to receive a new order for the part.
- Criticality: Classification of the part based on its impact on production (critical, essential, or non-critical).
By conducting regular inventory audits (at least annually, or more frequently for critical parts), you can identify discrepancies, optimize stock levels, and ensure the accuracy of your inventory management system.
2: Implementing a Centralized Inventory Management System
Manual inventory management processes are prone to errors and inefficiencies. Implementing a centralized inventory management system (IMS) streamlines operations and fosters data-driven decision-making. Here’s what an IMS can offer:
- Real-time Inventory Visibility: Provides a clear overview of current stock levels for all spare parts, readily accessible to authorized personnel.
- Automated Reordering: Sets reorder points for each part based on minimum stock levels and lead times, ensuring timely replenishment and preventing stockouts.
- Part Tracking and Reporting: Offers detailed tracking of each spare part, including its history, usage trends, and location within the warehouse.
- Data Analytics: Generates reports and insights to inform strategic decisions regarding stock levels, supplier selection, and forecasting future needs.
An IMS can be a cloud-based solution, on-site software, or a mobile application designed for ease of use on the go. When selecting an IMS, consider factors like scalability, compatibility with existing systems, and user-friendliness for your maintenance personnel.
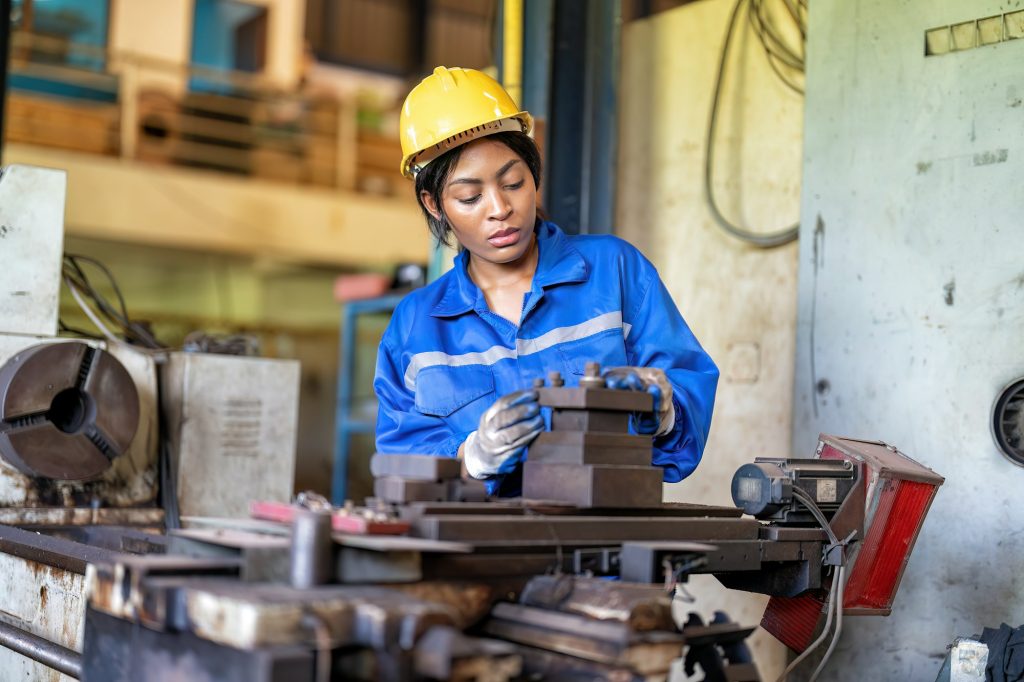
Utilizing Predictive Maintenance Techniques
Moving beyond reactive maintenance practices triggered by equipment failures, predictive maintenance leverages technology to anticipate potential issues before they occur. Here’s how predictive maintenance benefits spare parts inventory management:
- Proactive Part Identification: By analyzing vibration, temperature, and other equipment data, predictive maintenance techniques can identify components nearing failure. This allows for proactive ordering of the necessary spare parts before a breakdown happens.
- Reduced Emergency Orders: By anticipating part needs, you can avoid costly emergency orders with expedited shipping fees. Predictive maintenance allows for planning and optimization of spare parts procurement.
- Extended Equipment Lifespan: Early detection and repair of potential issues using spare parts can prevent major equipment failures and extend the overall lifespan of your machinery.
Common predictive maintenance techniques include:
- Vibration Analysis: Monitors vibration patterns in equipment to detect signs of wear and tear.
- Oil Analysis: Analyzes oil samples to identify changes in viscosity or the presence of metal particles, indicating potential component degradation.
- Thermography: Uses thermal imaging to identify abnormal temperature variations that may signal potential problems.
By integrating predictive maintenance with your spare parts inventory management system, you can ensure the right parts are available at the critical moment, minimizing downtime and maximizing equipment uptime.
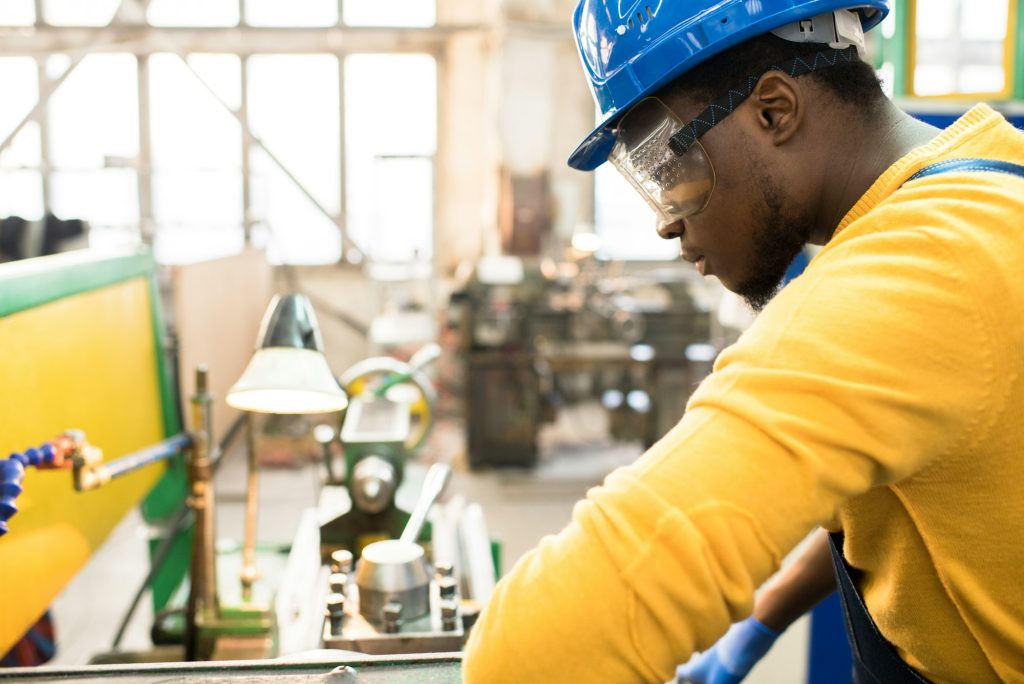
Establishing a Reliable Supplier Network
Maintaining a reliable supplier network for your spare parts is crucial for ensuring timely access to critical components. Here are key considerations for building a strong supplier network:
- Supplier Reputation: Select suppliers with a proven track record of quality, reliability, and on-time delivery.
- Competitive Pricing: Negotiate competitive pricing for spare parts while ensuring quality is not compromised.
- Service and Support: Choose suppliers who offer prompt and responsive customer service, including technical expertise and readily available replacement parts information.
- Lead Times: Understand lead times for different parts and consider working with multiple suppliers for critical spares to mitigate potential delays.
- Geographical Location: Evaluate the geographical location of your suppliers and potential impacts on lead times due to factors like distance and customs clearance procedures.
Developing strong relationships with a few key suppliers can be beneficial. This allows you to leverage volume discounts, receive priority service, and establish clear communication channels for efficient parts procurement.
Implementing a Strategic Stock Replenishment Plan
A reactive approach to replenishing spare parts, triggered solely by stock depletion, can lead to delays in acquiring critical components. Implementing a strategic stock replenishment plan ensures a proactive approach to maintaining optimal inventory levels. Here are key strategies for effective stock replenishment:
- ABC Analysis: Classify your spare parts based on their criticality (A – critical, B – essential, C – non-critical) and consumption rate (high, medium, low). This helps prioritize stock levels and replenishment strategies for high-impact parts.
- Minimum Order Quantity (MOQ): Negotiate minimum order quantities with suppliers that balance cost-efficiency with avoiding excessive stockholding.
- Safety Stock Calculation: Calculate the minimum stock level (safety stock) required for each part, considering lead times, potential demand fluctuations, and criticality. This ensures you have enough stock on hand to avoid disruptions during lead times.
- Reorder Point: Set a reorder point for each part based on safety stock and lead time. When inventory reaches this point, a new order is automatically triggered to maintain optimal stock levels.
By employing these strategies, you can ensure timely replenishment of critical spare parts while optimizing storage space and minimizing carrying costs for less frequently used items.
Setting Up a Robust Tracking and Monitoring System
Effective spare parts inventory management requires a robust tracking and monitoring system to maintain accurate data and ensure efficient operations. Here are key elements of a strong tracking and monitoring system:
- Part Movement Tracking: Track the movement of each spare part, from receiving through storage and issuance for maintenance activities. This provides transparency and accountability for inventory usage.
- Cycle Counting: Conduct regular cycle counts to verify the physical quantities of specific parts against system records. This helps identify discrepancies and maintain data accuracy.
- Barcoding and RFID Systems: Implement barcoding or Radio Frequency Identification (RFID) technology to automate part identification, tracking, and location management within the warehouse.
- Inventory Performance Metrics: Monitor key performance indicators (KPIs) such as stock accuracy, fill rates, and inventory turnover to assess the effectiveness of your inventory management strategies.
By establishing a comprehensive tracking and monitoring system, you gain real-time insights into your spare parts inventory, enabling informed decision-making and continuous improvement of your processes.
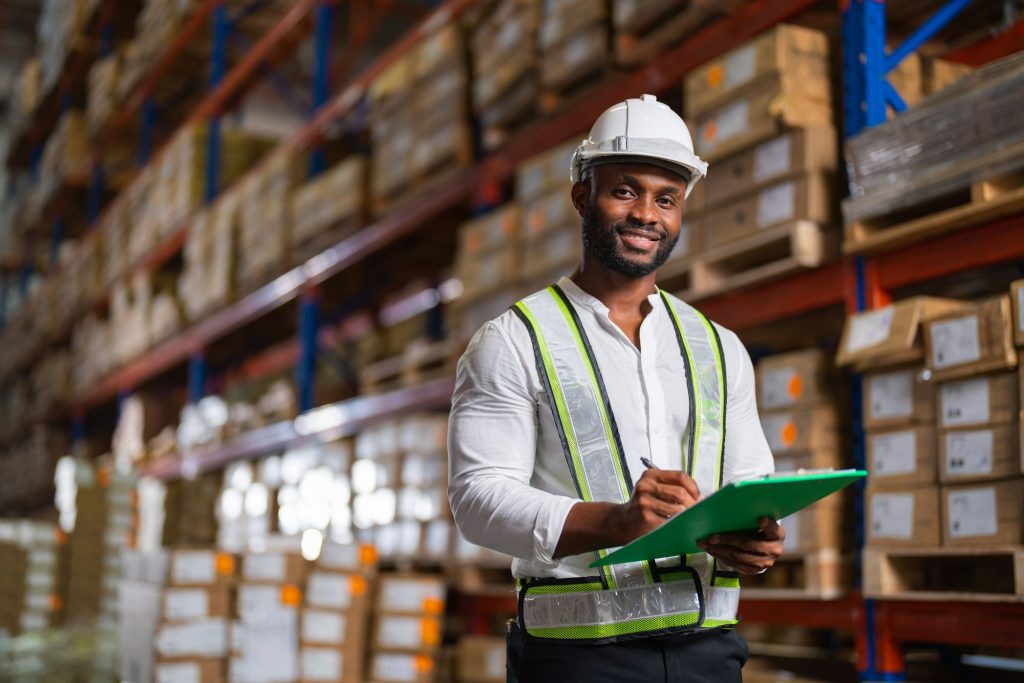
Regularly Reviewing and Optimizing Inventory Levels
Manufacturing environments and production needs can evolve over time. Regularly reviewing and optimizing your spare parts inventory ensures it remains aligned with current requirements. Here’s how to achieve this:
- Review Consumption Data: Analyze historical consumption data for each spare part to identify usage trends and adjust stock levels accordingly. Parts with declining usage may warrant lower stock levels, while those experiencing increased demand might necessitate higher safety stock quantities.
- Evaluate Equipment Updates: When upgrading equipment or incorporating new machinery, update your spare parts inventory to reflect the specific requirements of the new models.
- Supplier Lead Time Changes: Monitor and adjust reorder points and safety stock levels if supplier lead times change for any critical parts.
- Obsolescence Management: Identify and proactively address spare parts for equipment nearing obsolescence. This could involve selling surplus parts, negotiating extended support with the manufacturer, or finding alternative replacement components.
By regularly reviewing and optimizing your spare parts inventory, you can ensure it remains cost-effective and aligned with your evolving production needs.
Conclusion
Effective spare parts inventory management is a strategic practice with a significant impact on operational efficiency and cost control within manufacturing facilities. By implementing the seven best practices outlined in this guide, you can:
- Minimize downtime caused by equipment failures.
- Reduce reliance on expensive emergency orders.
- Optimize storage space utilization.
- Extend the lifespan of valuable equipment.
- Enhance overall production efficiency and profitability.
Investing in a robust spare parts inventory management system and fostering a data-driven approach will empower you to make informed decisions, achieve greater operational control, and ensure your manufacturing facility runs smoothly and efficiently.
Engage RPM as your Reliable Supply Partner:
Do you need a reliable partner for your industrial spares that aligns with your goal of elevating your operational efficiency? Look no further than Rotation and Precision Machines Limited (RPM).
For over ten years, RPM has been a trusted industrial engineering procurement company in Nigeria, partnering with global OEMs to provide comprehensive solutions for manufacturing factories. We offer a vast selection of industrial spares and engineering expertise to help you optimize your inventory, minimize downtime, and maximize your production potential.
Schedule a Free Consultation with RPM today!
We’ll help you identify cost-saving opportunities, ensure timely access to critical components, and empower you to achieve a more resilient and efficient operation. Contact RPM today and unlock the full potential of your manufacturing capabilities!