Introduction
Conveyor systems are mechanical devices that transport materials from one point to another. These systems are commonly used in manufacturing facilities to move raw materials, finished products, and other items throughout the production process. Conveyor systems can be simple or complex, depending on the needs of the facility. They may include belts, rollers, motors, and other components that work together to transport materials.
While conveyor systems can be highly efficient and improve productivity in manufacturing facilities, they can also pose significant safety risks if not operated properly. Conveyor systems can cause injuries such as cuts, burns, and even amputations if workers are not careful. Therefore, it is essential to follow safety guidelines to prevent accidents and ensure the safety of your employees.
Hazards Associated with Conveyors
Here are some of the most common hazards and accidents associated with using conveyor systems:
Entanglement: Loose clothing, hair, or jewelry can become entangled in the moving parts of a conveyor system, leading to serious injuries or even death.
Pinch points: Conveyor systems often have pinch points where two moving parts come together. If a worker’s hand or another body part gets caught in the pinch point, it can cause severe injuries.
Falling objects: If materials are not properly secured on the conveyor system, they can fall off and cause injuries to workers.
Electrical hazards: Conveyor systems are often powered by electricity, which can pose a hazard if the wiring is damaged or if workers come into contact with live wires.
Mechanical failure: If a conveyor system is not properly maintained, it can break down or malfunction, leading to accidents.
Overloading: If too much weight is placed on a conveyor system, it can become overloaded and break down, causing materials to spill and potentially injure workers.
Slip and fall hazards: Conveyor systems often have slippery surfaces, and workers can slip and fall if they are not wearing proper footwear or if the surface is wet or oily.
It is important to ensure that workers are trained on how to properly operate and maintain conveyor systems, and that safety protocols are in place to prevent accidents and injuries.
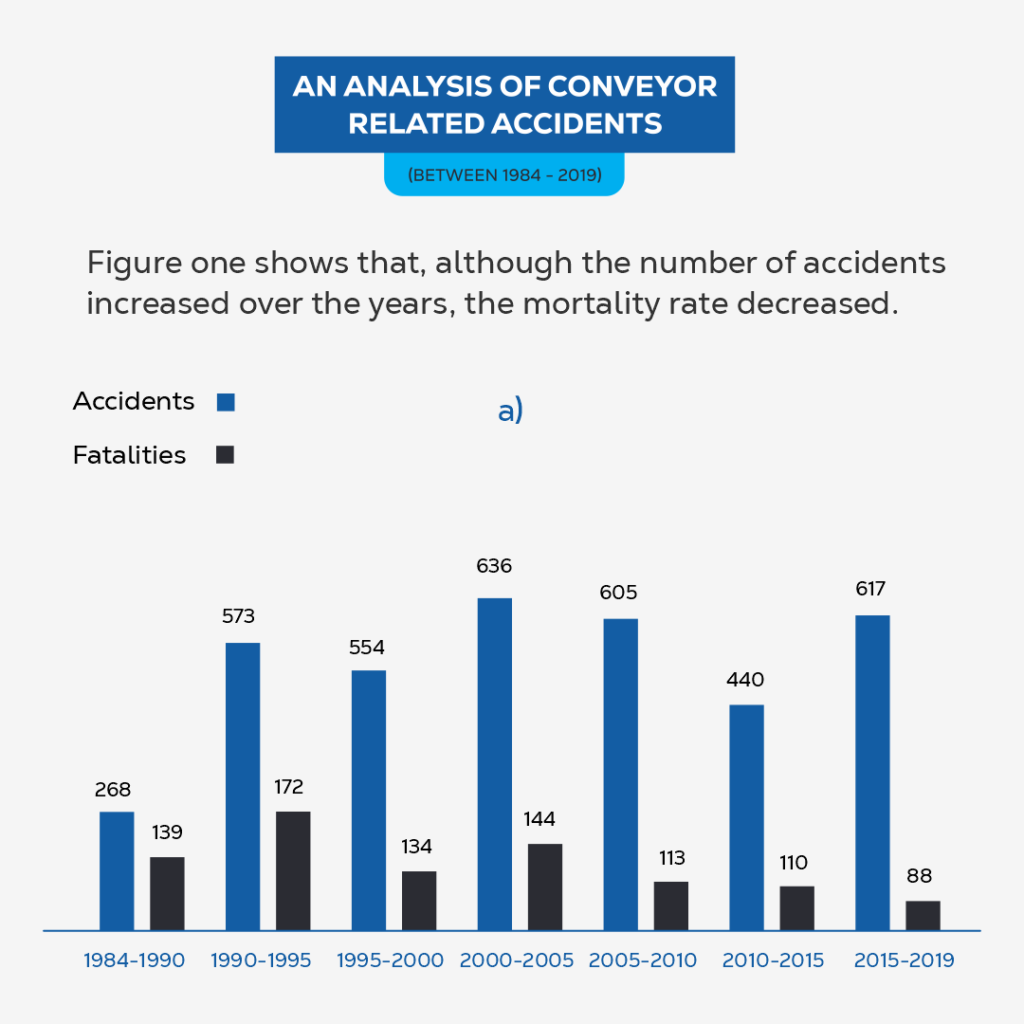
10 Essential Safety Guidelines for Operating a Conveyor System
There are two major areas that must be covered when addressing the safety of conveyor system,namely: design and installation and then operation.
Proper Design and Installation
Conveyor systems can cause injuries if they are not designed or installed properly. A poorly designed conveyor system can malfunction, leading to accidents. Therefore, it is essential to follow safety guidelines for conveyor system design and installation to ensure that workers are protected from potential hazards.
Here are some key considerations to make during the design and installation phases of a conveyor system.
- Conduct a risk assessment
Before designing or installing a conveyor system, conduct a risk assessment to identify potential hazards and develop strategies to mitigate them.
- Follow local regulations and standards
Be sure to follow local regulations and standards for conveyor system design and installation. These regulations and standards can vary by location, so it is essential to research and comply with them.
- Use safety guards and barriers
Install safety guards and barriers to prevent workers from coming into contact with moving parts or falling objects.
- Ensure proper clearance
Ensure that there is proper clearance between the conveyor system and other equipment or structures to prevent accidents.
- Conduct regular maintenance
Conduct regular maintenance on the conveyor system to ensure that it is functioning correctly and to identify potential hazards.
Wear personal protective equipment (PPE)
Wear personal protective equipment (PPE) such as gloves, safety glasses, and steel-toed shoes to protect against potential hazards.
Personal protective equipment (PPE) is essential for conveyor system operators to protect against potential hazards. Here are some essential PPE items for conveyor system operators:
- Gloves
Gloves can protect against cuts, scrapes, and other injuries when handling materials on the conveyor system.
- Safety glasses
Safety glasses can protect against flying debris and other potential hazards.
- Steel-toed shoes
Steel-toed shoes can protect against foot injuries if a worker’s foot is caught in the conveyor system.
- Hard hats
Hard hats can protect against falling objects or materials that are being transported on the conveyor system.
By providing appropriate PPE to conveyor system operators, you can reduce the risk of accidents and ensure that your workers are protected from potential hazards.
Follow lockout/tagout procedures
Follow lockout/tagout procedures to ensure that the conveyor system is shut down and de-energized before performing maintenance tasks.
Use caution when working near the conveyor system
Use caution when working near the conveyor system to avoid coming into contact with moving parts or materials.
Report any safety hazards
Report any safety hazards to your supervisor or safety manager immediately
Use emergency stop buttons and follow emergency procedures in cases of emergency
Emergency stop buttons and procedures are essential for conveyor systems to ensure that workers can quickly shut down the system in case of an emergency. Let’s consider some guidelines for emergency stop buttons and procedures:
- Install emergency stop buttons
Install emergency stop buttons at various points along the conveyor system so that workers can quickly shut down the system if necessary.
- Train workers on emergency stop procedures
Train workers on emergency stop procedures so that they know how to use the emergency stop buttons and what to do in case of an emergency.
- Conduct regular drills
Conduct regular emergency stop drills to ensure that workers are familiar with the emergency stop procedures.
- Develop Lockout/Tagout Procedures
Lockout/tagout procedures are essential for conveyor systems to ensure that workers are protected from potential hazards during maintenance tasks.
Develop a lockout/tagout program that outlines the procedures for shutting down and de-energizing the conveyor system during maintenance tasks.
Also, sensitize workers on lockout/tagout procedures so they know how to safely shut down and de-energize the conveyor system.
Lastly, use lockout/tagout devices to prevent the conveyor system from being energized while maintenance tasks are being performed.
Conduct regular maintenance
Conduct regular maintenance on the conveyor system to ensure that it is functioning correctly and to identify potential hazards. Inspect the belts, rollers, pulleys, and other components for signs of wear, debris buildup, or any loose or damaged parts. Cleaning and lubrication of the conveyor is also an aspect of maintenance. Promptly address any identified issues or damaged parts. Repair or replace worn-out or damaged components to prevent further problems and potential breakdowns.
Observe Safety Guidelines for Handling Materials on Conveyor Systems
Handling materials on a conveyor system can pose significant safety risks if not done with care. Here are some essential safety guidelines for handling materials on conveyor systems:
- Do not overload the conveyor system
Do not overload the conveyor system to prevent it from malfunctioning or breaking down.
- Use proper lifting techniques
Use proper lifting techniques when handling materials on the conveyor system to prevent injuries.
- Keep hands and clothing away from moving parts
Keep hands and clothing away from moving parts to avoid getting caught in the system.
- Use caution when working near the conveyor system
Use caution when working near the conveyor system to avoid coming into contact with moving parts or materials.
Train Employees on Conveyor Safety Procedures
Conveyor system safety training is essential to ensure that workers are aware of potential hazards and know how to operate the system safely. Here are some tips for conveyor system safety training:
- Provide initial training
Provide initial training to all employees who will be working with the conveyor system.he
- Provide refresher training
Provide refresher training on a regular basis to ensure that employees are up-to-date on safety guidelines and procedures.
- Tailor training to specific job roles
Tailor training to specific job roles to ensure that employees are trained on the specific hazards and procedures that apply to their job.
- Use hands-on training
Use hands-on training to ensure that employees know how to operate the conveyor system safely.
By providing comprehensive safety training to employees, you can reduce the risk of accidents and ensure that your workers are aware of potential hazards and know how to operate the system safely.
Continuous Improvement and Monitoring of Conveyor System Safety
Continuous improvement and monitoring of conveyor system safety are essential to protect workers from potential hazards. To monitor the conveyor system for sustained safety, follow the steps below:
Conduct regular safety audits
Conduct regular safety audits to identify potential hazards and develop mitigation strategies.
Implement safety improvements
Implement safety improvements based on the results of safety audits.
Monitor safety performance
Monitor safety performance to ensure that safety guidelines and procedures are being followed.
Encourage worker feedback
Encourage worker feedback to identify potential hazards and develop strategies to mitigate them.
Conclusion
In conclusion, safety guidelines for operating a conveyor system are essential to ensure the safety of your employees and prevent accidents. By following the guidelines outlined in this article, you can reduce the risk of accidents and ensure that your conveyor system is designed, installed, operated, and maintained with safety in mind. Remember to provide appropriate PPE to conveyor system operators, install emergency stop buttons and lockout/tagout procedures, and provide comprehensive safety training to employees. By continuously improving and monitoring conveyor system safety, you can ensure that your workers are protected from potential hazards and that your manufacturing facility operates safely and efficiently.
Implement these safety guidelines for operating a conveyor system to ensure the safety of your employees and prevent accidents. Contact us to learn more about how we can help you improve safety in your manufacturing facility.